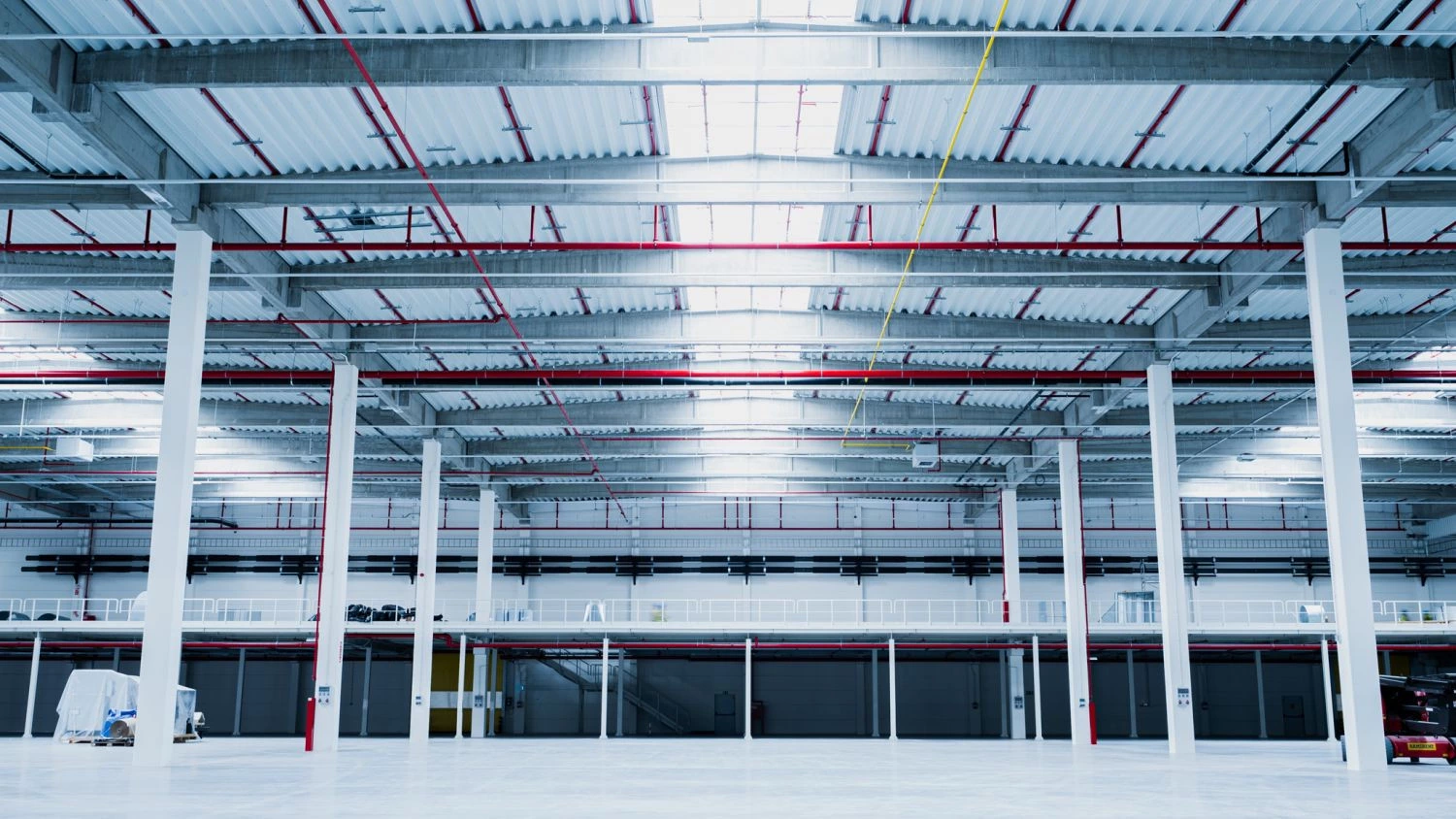
Warehouse tenants are adopting increasingly advanced technologies to meet client requirements, but at the same time, they also need to be mindful of employee wellbeing. Standard buildings in industrial parks are not enough. Companies need customised warehouses and tailor-made solutions, say experts from Newmark Poland.
At the end of June 2024, BTS (build-to-suit) facilities accounted for over a quarter of Poland’s total industrial stock or approximately 9 million sqm. Nearly 450,000 sqm was under construction. “Despite lower new warehouse supply levels in recent years, demand for tailor-made space remains strong. According to Newmark Polska statistics, last year saw more than 931,000 sqm leased in BTS warehouses, with nearly 460,000 sqm transacted in the first half of this year”, says Michał Kozar, Associate Director, Industrial and Warehouse Department, Newmark Polska. “The largest transaction in this period was an e-commerce company’s lease for over 265,000 sqm of BTS space in P3 Wrocław. Since the beginning of last year, lease transactions in excess of 100,000 sqm have also been finalised by Inditex (DL Invest Psary), Raben (CTPark Warsaw West), and LPP Logistics (Bydgoszcz Białe Błota Logistics Center).”
Lubuskie for e-commerce, Silesia for manufacturing
Companies have, for several years, focused on acquiring leasehold or freehold BTS warehouses in such provinces as Silesia (nearly 180,000 sqm – this represented the highest BTS supply level in 2023), Kuyavia-Pomerania and Lubuskie.
“Leading BTS locations clearly demonstrate which sectors most often need customised spaces. The BTS market has for years been driven by e-commerce which expanded at pace in Kuyavia-Pomerania and Lubuskie on the back of workforce availability and relatively low labour costs. Another advantage of Lubuskie is its proximity to Germany”, explains Jakub Kurek, Head of Industrial and Warehouse Department, Newmark Polska. Notable projects in this region include the construction of a BTO warehouse developed on a 23-hectare plot for TK Maxx in Sulechów. Spanning more than 61,000 sqm, it is the largest distribution centre across continental Europe sending shipments to over 250 TK Maxx stores in Poland, the Netherlands, Austria and Germany.
“Faced with growing customer requirements, e-commerce market players needed warehouses meeting precise specifications in terms of location, size, clear height and equipment, and cutting-edge technology. Such e-commerce giants as Zalando, Hermes Fulfilment and Amazon opted to lease warehouses of up to 250,000 sqm”, says Michał Kozar. “Due to high inflation and lower consumer spending, e-retailers no longer need big-box facilities, but by no means have they disappeared from the warehouse or BTS market”.
Today, food retailers such as Auchan, Intermarché and Stokrotka are major BTS market players. Special adaptations are required to ensure appropriate storage conditions for food products in terms of temperature and humidity and to meet strict sanitary regulations. This has led to the growing popularity of BTO warehouses in this sector, with this model embraced by such retail chains as Dino, Lidl and Biedronka.
BTS projects are also popular with manufacturers whose favourite location for manufacturing plants is Silesia. However, in contrast to e-commerce, manufacturers need far smaller facilities averaging 20,000-30,000 sqm, up to 50,000 sqm.
It all starts with location
Despite a diverse availability of ready-to-occupy buildings, their space is not what manufacturers, food retailers, e-retailers and companies from many other sectors may be looking for. Adapting a standing facility to individual needs and specifications may be too costly and thereby unprofitable but mostly unfeasible. “Tenants opting for a BTS or BTO warehouse may decide on many aspects of a project, starting from site selection. A warehouse can be built on the plot of a developer or a client – in the latter case, it will be a BTO project. Tailor-made facilities are also constructed as standalone buildings within large logistics parks or on adjacent fenced sites. One of the first decisions a client needs to make together with an adviser and developer is choosing the right plot, size, shape and location”, says Michał Kozar. “A BTS warehouse developed for Dywidag Systems in Panattoni Park Ruda Śląska II is particularly noteworthy. Dywidag Systems, a leading European supplier of post-tensioning and cable solutions for bridges, whom we had the pleasure of representing, needed a very long facility that would accommodate an almost 300-metre long gantry crane. We knew from the start that it would be very difficult to find a warehouse of the right size and specifications in a multi-let park. In the end, our client opted for a tailor-made project to have a say on its specifications, technologies and many other details during the construction stage”, explains the expert from Newmark Polska.
Say what you need
BTS projects also come with a risk. Once a tenant has relocated to a different building upon lease expiry, the developer of a vacated bespoke facility may experience difficulties with leasing it to others. This is why a company opting for a BTS warehouse must be ready to sign a contract for 10 or more years. The more spending and unique technological adaptations are needed, the longer the lease on such a property will be required.
Costs are another matter. Numerous client-specific adaptations and guidelines will usually make a BTS/BTO warehouse more costly to build. “Companies choosing to have a BTS warehouse built report diverse needs - be it a specific location, a special plot size, a building’s height or deployment of cutting-edge technological lines in a production plant. BTS warehouse rents also vary, depending on how the landlord and the tenant contribute to fit-out costs. BTS projects are more complicated to deliver and require attention to every detail, so we support our clients throughout the development process. With a tailor-made project, tenants enjoy flexibility, greater capabilities and the upper hand in negotiations, but they also need to be mindful of each and every detail”, says Jakub Kurek, Newmark Polska.
When is a BTO warehouse the right option?
One of the first steps in project delivery is to prepare a budget. If costly technologies are to be deployed, fit-out costs are, in fact, likely to outstrip the value of a building. This sometimes happens. A client may then restart negotiations from the beginning and opt for a BTO project but, of course, does not have to. It is for the client to decide with regard for its funds available and corporate policy”, says Michał Kozar. “Some companies opt for BTO warehouses right from the start but they have options to choose from here too: build a facility on their own with their team and a general contractor or contract a developer to handle the entire development process - from securing an appropriate plot through to design, construction and turnkey delivery.
A new warehouse in 10 months or later
If a tenant meets basic criteria - they need a warehouse for 10 or more years and submit requisite financial guarantees - developers are very willing to build customised warehouses. Unlike logistics parks, BTS/BTO projects are a safe business for developers.
“Faced with challenging macroeconomic conditions, developers have become even more willing to commit to BTS developments. Every large developer has its own BTS project team”, says Michał Kozar, Newmark Polska, adding that the turnaround time is 8-10 months for a traditional facility and usually longer for a BTS project. “There are many factors at play. Some projects may be a perfect match for a developer’s plot, thereby shortening the preparation process. If not, an alternative suitable plot of land will have to be secured or the one that is available adapted accordingly. The last stage, which is the warehouse fit-out, is also very time-consuming - it requires ordering and waiting for the delivery of systems, cranes, cold stores, freezers and other items.
BTS projects are doing well
According to Newmark Polska, demand for customised warehouses will grow as the entire market advances. “BTS development has strong potential in Poland but is dependent on the country’s overall geopolitical and economic situation. Companies from leading BTS occupier sectors such as manufacturing, retail and e-commerce are likely to be attracted to invest in Poland by business-friendly tax and customs regulations, as well as the country’s political and economic security and stability”, concludes Michał Kozar.