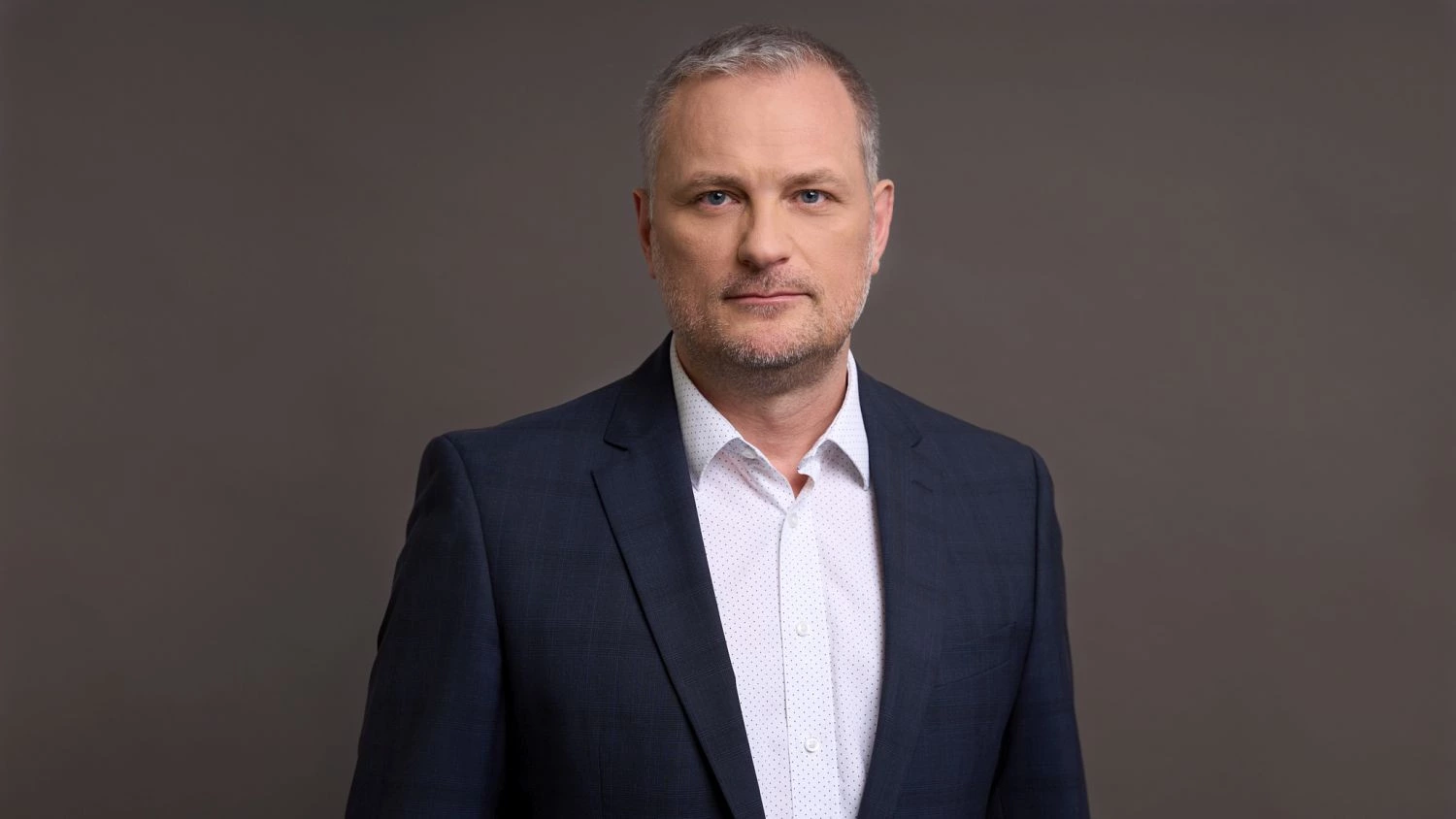
Krzysztof Trembowski, Senior Project Director at cmT Group has talked to Property Forum about the demand for BTS projects, the rapid development of energy-saving technologies and rising reliance on the prefabricated elements.
What share of your order book currently consists of warehouse projects? Like your competitors, have they recently given way to residential developments?
While the majority of our revenue stems from industrial projects, we have been active in the warehouse sector for many years. In addition to performing investor supervision, we conduct technical audits for market transactions’ needs, provide warranty inspections, and perform technical analyses aimed at enhancing the energy efficiency of existing facilities. Currently, we estimate that warehouse-related projects account for 5-7% of our overall revenue. Thus far, we have not observed a decline in warehouse orders in favour of residential developments. However, we do foresee potential shifts, driven by the entry of large investment funds that may target substantial residential projects, such as student housing and rental apartments. In such cases, we can be a natural partner for both project execution and transactional support in the purchase and sale processes.
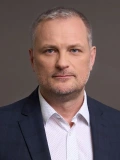
Krzysztof Trembowski
Senior Project Director
cmT Group
BTS, BTO, or perhaps still speculative Big Boxes? What type of facilities do you think will be the most popular in the near future?
From our perspective, BTS (Build-to-Suit) developments already dominate the market, and we do not foresee this changing in the short term. Advanced technologies are becoming increasingly important in large-scale projects, particularly for high-storage facilities, stringent hygiene standards for stored goods in dedicated warehouses, and solutions that promote energy efficiency—both during the construction phase and throughout the facility’s lifecycle. Speculative developments always involve compromises between cost and market consensus on tenant needs. However, with the growing emphasis on ESG considerations, the ability to customize large-scale facilities to the specific needs of the end user will become increasingly important. In BTS projects, such customizations can be analyzed during the design phase, ensuring decisions are aligned not only with individual ESG strategies but also with short- and long-term economic objectives.
High prices for electricity and energy raw materials have been a constant feature of the real estate landscape in our country for several years now. How much emphasis do the investors who work with you place on energy efficiency?
The war in Ukraine significantly impacted energy prices, and since 2022, energy efficiency studies have become a critical element in our services. We are receiving numerous inquiries related to energy audits and facility modernization aimed at improving energy performance. This trend is also evident in new developments, where energy efficiency is becoming increasingly important for both investors and contractors. We are constantly learning and adapting to new solutions, as we aim to be well-prepared for these challenges. I believe that an openness to new technologies, combined with respect for traditional construction processes, will be crucial for remaining competitive in the coming years. Buildings’ modernization, particularly in terms of anticipating its effectiveness and profitability, presents a major challenge. Technologies that were state-of-the-art ten years ago will likely be obsolete in another decade. We’ve seen considerable advances in areas like heating and cooling systems in recent years.
It’s important to note that energy efficiency isn’t just about photovoltaic panels or heat pumps. A customized approach to maximizing the efficiency of individual systems can also be crucial. For example, installing louvres on a building’s southern façade—a relatively small investment—can significantly reduce heat accumulation, leading to lower energy consumption. Nowadays, we can calculate these factors with great precision, allowing investors to make informed decisions that are both cost-effective and energy-efficient.
What non-standard, innovative solutions - in terms of design, materials and technology - do you implement in the buildings you construct?
Unfortunately, we are unable to disclose details about some of the solutions due to confidentiality agreements. However, what was considered innovative just a few years ago has now become standard practice. For instance, heat pumps and photovoltaic installations are now commonplace. We leverage our analyses and data to identify optimal and rational solutions for investors. One of example involves one of our photovoltaic farms, where we devised a system to manage water that accumulated under the farm auxiliary installations, ultimately repurposing it for the farm and its neighbouring irrigation.
You also carry out property audits and technical inspections. Is the ‘Great Wave of Renovation’ associated with changes in the EU legal system already approaching Poland?
In fact, this wave has already arrived. We collaborate with the largest investors in the market and have observed significant changes in their approach. In our market, major investors are already setting new trends to be followed and supported by engineering and construction crews. As an engineering company, we are continuously educating and evolving to meet the changing demands of our clients. A prime example is the integration of competencies related to the EU taxonomy. Today, we are equipped to prepare all necessary documentation, including carbon footprint calculations, using cutting-edge software and company experts in the field.
cmT Poland employs a number of people with experience in international markets, including Africa, the USA and the Far East. While it’s difficult to directly compare these markets with Europe, are there any practices from these regions that you would apply to Poland in terms of industrial facility development?
Such international experience is invaluable. It enables us to operate effectively in diverse environments and quickly adapt investor expectations to local conditions, leading to reduced project timeframes and costs. This, in turn, enhances the quality of our services and reinforces our position in the market. Most of our clients are foreign investors, so this kind of experience is crucial.
Regarding the market outlook, we expect an even greater reliance on prefabricated elements in industrial facility construction. This approach has proven highly effective in certain international markets, and investors in Poland increasingly expect similar levels of efficiency. This expectation also stems from an awareness of potential changes and/or improvements in the use of industrial facilities under construction. Their implementation would be quite complicated in the case of custom cast-in-place structures.
As for our internal innovations, we take pride in our advancements. At cmT, we implemented internal tools that communicate with technical and technological documentation based on BIM (Building Information Modelling) culture and standards some time ago. And BIM is now a must-be component in construction processes. In addition, we are constantly improving the tools we use to manage projects and to create reports and technical expertise, for internal communications and systems that allow our engineers to use the data and knowledge stored in our archives. This continuous learning and innovation ensure we remain competitive with major global consulting and project management firms.