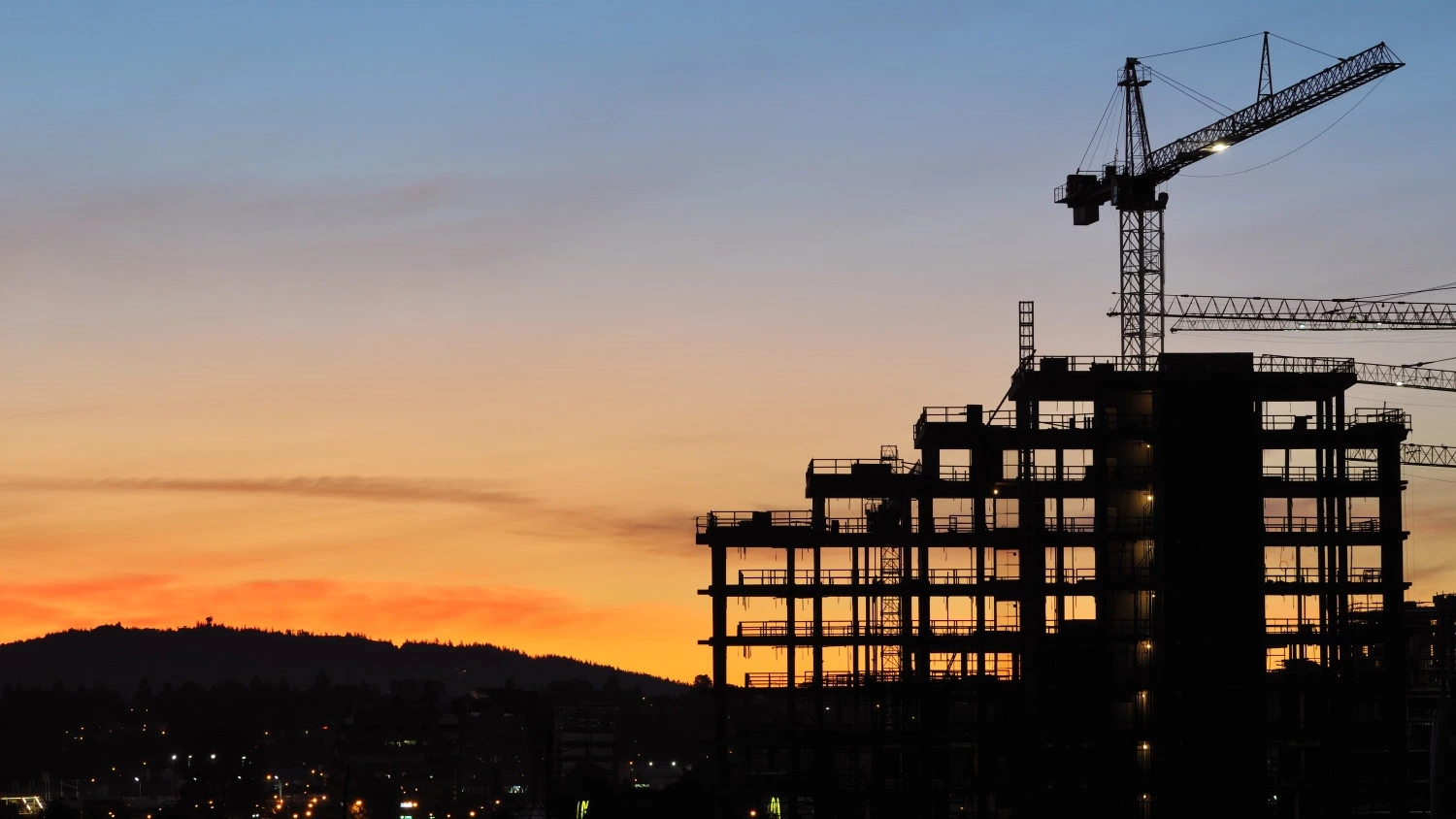
Since the onset of the full-scale invasion, the proportion of imports on Ukrainian construction sites has remained relatively stable, with any monetary growth primarily attributable to fluctuations in exchange rates. The Ukrainian Real Estate Club has convened insights from representatives of various development companies to conduct a thorough analysis of the current share of imports, the evolution of procurement strategies, and the materials and components that predominantly remain imported.
Share of imported materials: from 12% to 40%
The proportion of imported materials in construction varies significantly based on project classification, geographical location, and the strategic approaches adopted by developers. For instance, at Gazda’s Park Land residential complex in Uzhhorod, this share is approximately 12%. Conversely, projects undertaken by Alliance Novobud in the Kyiv region report an estimated import share ranging from 30% to 40%. Specialists from Intergal-Bud, operating in Kyiv and Lviv, indicate that 80% of the materials and components utilized in their projects originate from Ukraine. Imported goods constitute about 20% of their total materials, predominantly consisting of elevator equipment due to the limited number of competitive manufacturers in this sector within Ukraine.
In the construction of residential buildings and hotels, the share of imported goods can reach up to 30%, primarily comprising finishing materials. “We procure all other materials from Ukrainian producers and suppliers,” asserts Mark Marchenko, CEO and founder of SENSAR Development based in Zaporizhzhia.
Overall, industry experts and construction directors report that the share of imported building materials within the Ukrainian construction market has escalated from 12-14% in 2021 to 23% in 2023, with projections indicating it may approach 25% by 2024.
Key imported items
Market participants have identified several segments where imported materials remain indispensable:
- Elevator equipment
- Facades and thermal insulation
- Heating and communication systems
- Window profiles and glass
- Internal networks
These categories frequently lack competitive alternatives among Ukrainian producers due to a dearth of manufacturing enterprises or stringent product quality requirements. Historically, there have been no operational facilities for glass or electrical equipment production; however, new PVC and cement production facilities have emerged as a positive development.
Marianna Bihunets, an industry expert, notes: “In our projects, the most significant imports by value include internal networks (such as electric boilers from Bosch (Germany), boilers from Drazice (Czech Republic), underfloor heating combs from Danfoss (Denmark), underfloor heating tubes from KAN (Poland), and wi-fi temperature controls for heating systems from DEVIreg (Denmark)), as well as playgrounds and artificial turf, facades (utilising Rockwool and Greinplast finishing systems from Poland), and elevators from Otis (Spain).”
Among the primary factors contributing to the increasing share of imports within construction sites are complex logistics, extended delivery times for imported goods, and rising costs driven by currency appreciation, inflationary pressures, and transportation expenses. This trend is further exacerbated by the necessity for numerous Ukrainian companies to suspend or limit production activities, relocate operations, or increase prices due to military actions. In contrast, foreign counterparts have largely maintained their pricing structures. Additionally, challenges related to port infrastructure and the reconfiguration of logistics networks continue to constrain the volume of imported materials.
Support for domestic producers
In spite of these challenges, a significant number of developers are committed to maximising their utilisation of Ukrainian materials. Experts observe that local producers are actively responding to market demands by developing competitive products. Notably, in the realm of ceramic tiles for bathroom or facade decoration, Ukrainian manufacturers are offering high-quality products that rival imported alternatives in both technical specifications and design aesthetics.
Furthermore, Ukrainian manufacturing facilities are equipped to produce bespoke products tailored to individual client specifications—featuring unique patterns, textures, and shades. The modern production lines employed by domestic enterprises enable them to manufacture competitive products that adhere to stringent quality standards.
Moreover, collaboration with Ukrainian suppliers facilitates predictable delivery timelines, more advantageous contractual terms, and reduced logistics costs—all contributing positively to the efficiency of construction processes.