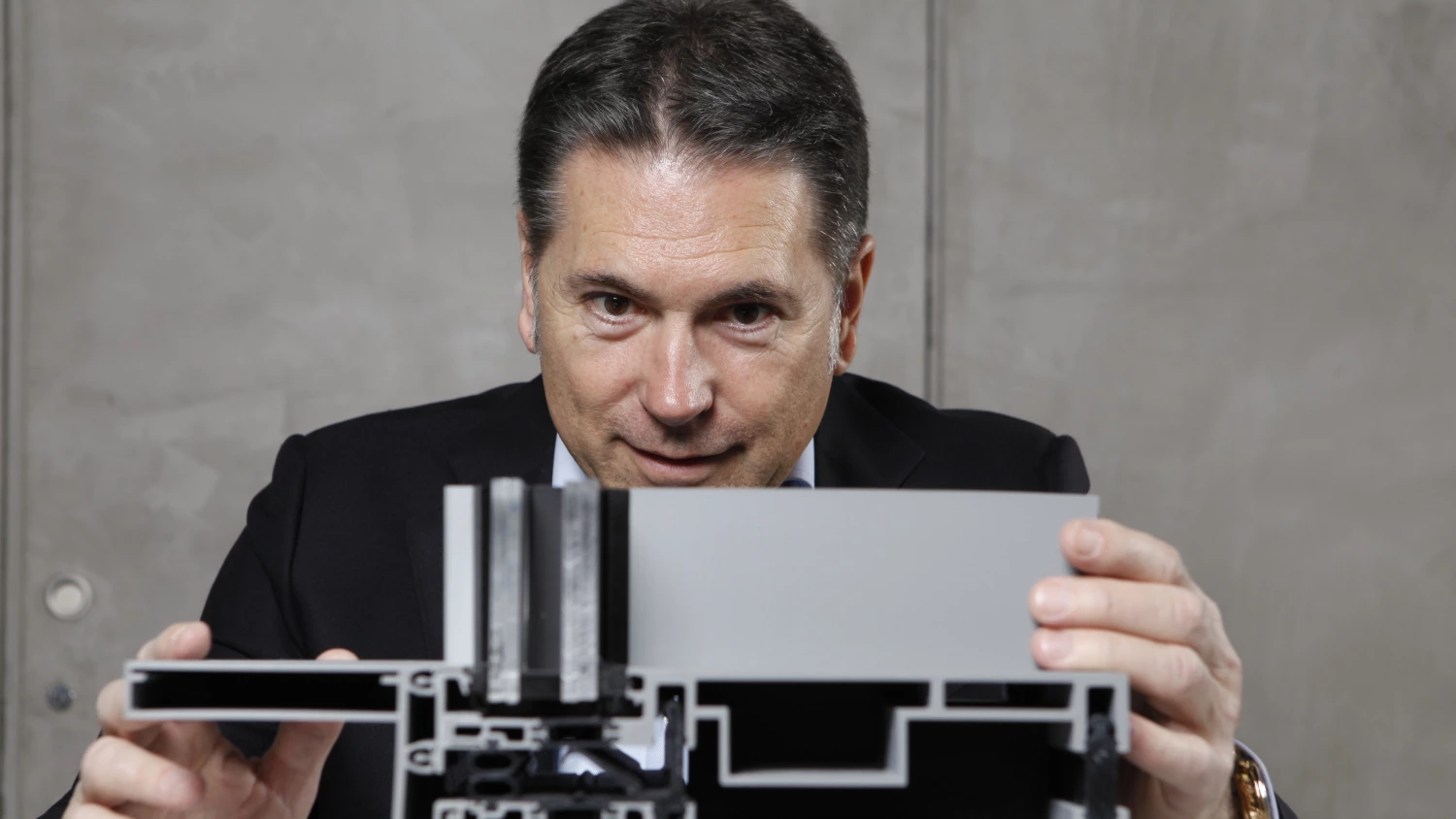
Attila Beer, Country Manager at Alukönigstahl Romania & Republic of Moldova, spoke to Property Forum about the company’s growth plans for 2024 and the outlook for the residential sector, which generated 80% of its sales last year.
This interview was first published in Property Forum’s annual listing of "The 50 most influential people on Romania’s real estate market”.
How did Alukönigstahl Romania’s business develop last year and what are your prospects for 2024?
Last year tested our perseverance. Although we started well with sales, after the first quarter we noticed a general slowdown in decision making. We had contracts signed in May and not started until August. Decisions made in our favour in August and orders launched in November.
The whole team mobilised again in Q4 and we managed to achieve our forecasts, again exceeding €20 million in turnover. For the current year we are targeting a minimum of 5% growth.
Given the uncertainty in the eurozone, the downward trend in raw material prices and the challenges caused by the difficulty in finding dedicated staff, this year will also challenge us.
Which segments generated the highest demand for Alukönigstahl Romania in 2023 and what are your expectations for 2024?
Residential construction generated the largest share of turnover in 2023 as well, with a share of around 80%. The rest of the sales was covered by the retail segment, for example with Dedeman stores, Kaufland, Lidl and industrial halls.
We have also been involved in medium-sized office building projects such as Arghezi Office and AFI Loft in Bucharest, IT Perspective Sibiu, Bosch headquarters in Cluj and Hamilton Timisoara headquarters.
To these were added other mixed-use buildings, including office and residential. This year we have several large office projects in the pipeline that we believe have the best chance of reaching the completion phase in 2025. Most existing residential projects are in the medium quality category.
On the other hand, there are announced public projects (hospitals, gyms, educational spaces) that should start this year, and our task is to win as many of them as possible.
In which projects is Alukönigstahl Romania supplying aluminium, steel and PVC systems this year?
I can mention ONE High District, ONE Floreasca Tower in Bucharest and Oxygen in Cluj Napoca. These are large residential projects for the premium market, where we started delivering aluminium systems in 2023 and will complete them this year. To these we are adding, for the time being, Cortina North (D body), Nusco City – phase 2 in Bucharest and Tomis Tower in Constanța.
These are large projects. We also have other, smaller projects and individual houses in our portfolio. For the H4L residential complex we will also deliver Schüco Living PVC profile systems. In terms of steel profile systems we most commonly deliver fire resistant door solutions to various types of buildings, from stadiums to hospitals.
What are raw material prices like at the beginning of 2024 and what factors will influence costs in this area?
There are many aspects influencing the price of raw materials: low demand in Western Europe and the continuing downturn in the Chinese construction industry are factors that influence the price favourably from the buyers’ point of view. But uncertainty in the Middle East, the US elections and the war in Ukraine are risk factors. Certainly, by mid-year, we expect the downward trend to continue.
How do you help real estate developers who want to increase the sustainability of their projects?
Last year, our partner Schüco launched the Carbon Control programme, designed to reduce the carbon footprint of the building construction envelope. This is a concept with modular solutions for investors, project developers and building contractors that supports compliance with EU taxonomies. Reducing the carbon footprint starts at the design stage, by choosing the optimal carbon footprint solutions.
Our products thus minimise the carbon footprint of the building envelope throughout the entire life cycle – from design to demolition. In addition to choosing the optimal façade construction or an appropriate façade system, the use of optimised materials also has a significant impact on a building’s carbon footprint.
Our tools and services provide relevant certification and documentation to ensure an efficient construction, renovation and operation process.
How do you support building owners who want to renovate or transform a project?
This advice depends very much on the owners’ expectations: what is the level of quality, who they want to address with the services in the building, etc. We have the best technical team and the best products in the field in which we operate. The first step in renovation would be to prepare a shortlist of priorities, then a technical project. The first step is the owner’s, then the architect intervenes and we come up with the solutions.
A very important aspect is the allocation of the necessary funds. We also have cost estimation services according to the technical requirements.
What significant trends do you see in your market?
I see a segmentation of companies active in the building envelope sector. Large firms that were active in large office projects are finding it difficult to adapt profitably to current realities. Residential projects require a different approach to office or hotel projects. And developers’ habit of treating the price of materials, workmanship and installation separately is driving facade players into the unprofitable zone.
On the other hand, large PVC window manufacturers are reorienting themselves towards the project market and successfully offering through their dealers. Compared to firms that used to work on projects, these companies are better organised in terms of production. Their success can also be verified by the financial data published on their official pages.
How open are Romanian developers to innovative technical solutions that can make projects more efficient in the long term?
In general, developers are very aware of technical innovations in the construction sector and are receptive. The challenge is to find the right balance between quality, innovation and profitability. I can say that often the profit motive wins out over sustainability and quality. We all have a lot of room for improvement in this business and that makes me optimistic: there is a lot of work to be done in my next few active years.