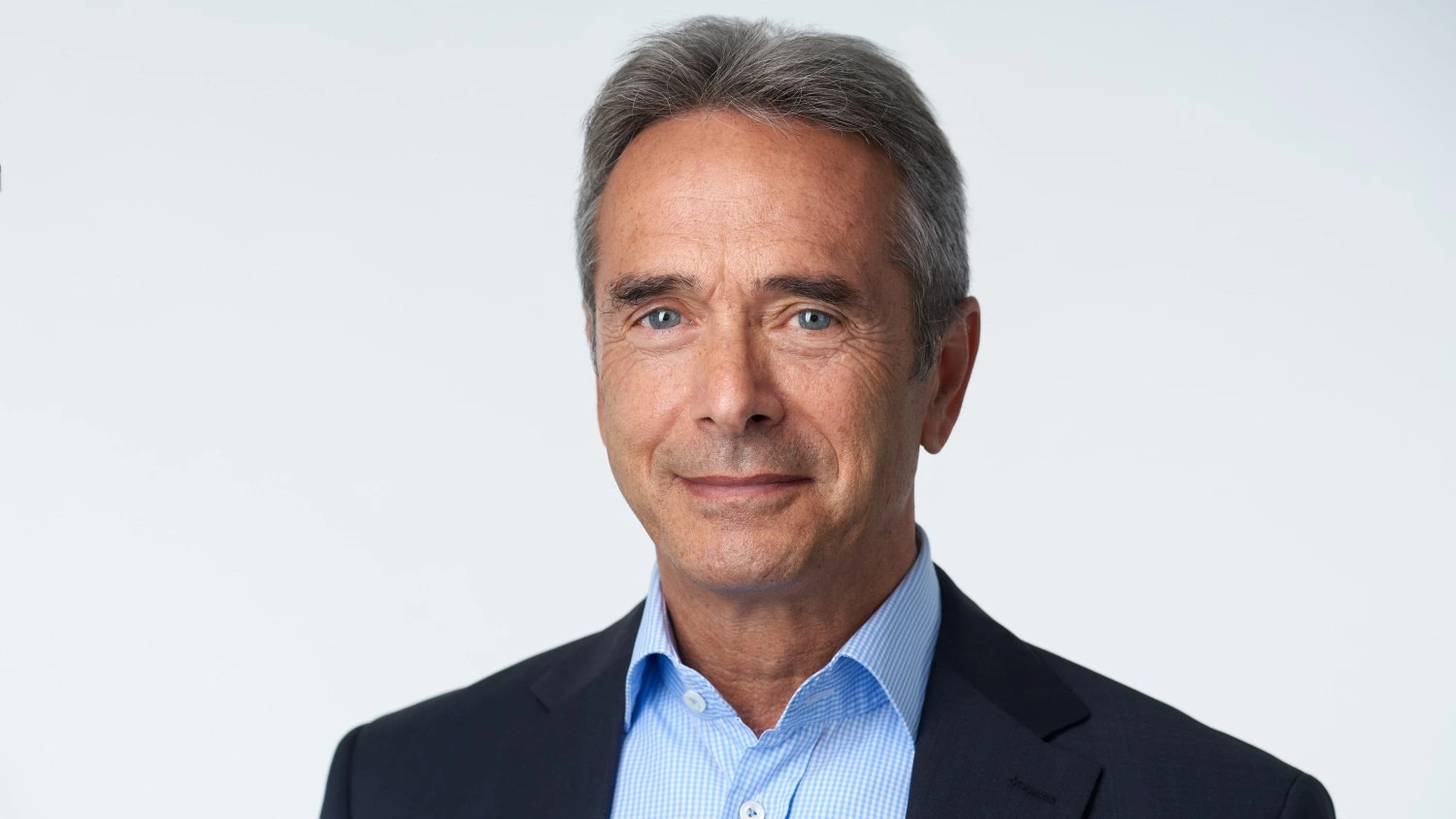
Some forms of government support may temporarily ease the current tough conditions for part of the construction sector in Hungary. But companies may not count on outside help only. All have to invest in new technologies and extend their in-house competencies, especially to reach ESG compliance, says Pál Dános MRICS, Associate Partner at KPMG Hungary in an interview with Property Fourm.
In which ways can the construction industry handle the continuingly volatile macroeconomic environment?
According to our recent survey, 83% of respondents—all of whom lead major industry companies—believe that improving the accuracy of estimating the amount of materials and equipment used are important tasks, since these account for a significant proportion of project costs. Another key imperative for project owners and developers is to achieve better contractual protection. Of course, in general, construction companies would naturally prefer to move toward flexible contracting terms and job pricing.
Among contractors, a dramatic shift away from fixed-price and guaranteed maximum-price contracts is seen for major projects. They are no longer willing to assume primary responsibility for performance risks, and project owners will therefore need to adjust how they control development projects. This, combined with increased inventory size — to create supply chain resilience —may decrease the risk for both general contractors and subcontractors, which may have an impact on their financial planning of projects.
We don’t know yet how these conflicts might damage developer and contractor relationships at a time when the two parties should be working more closely together to enable their risk management. In my view, the current economic decline would be advantageous for those companies that can deliver the best quality projects. Client satisfaction supported by proven reliability could keep the most experienced and innovative contractors in the marketplace for the next few years.

Pál Dános MRICS
Associate Partner
KPMG Hungary
Pál is an Associate Partner of the firm in the Budapest office and joined KPMG in 1998. He started his career as an architect-planner. Pál has been working for the past thirty-five years in the real estate industry as a planner, appraiser and advisor. He has been a member of RICS since 2000. Pál speaks Hungarian and English. More »
Many companies often follow the general mood and raise their prices, blaming inflation. How long they can do this without losing clients due to high prices?
This is a sensitive issue. Inflation and the tough economic environment influence both developers and potential buyers. One key decision factor when considering a property acquisition is the purpose of the potential buyer, whether it is for investment or use. Traditionally, investing in real estate offers protection against inflation.
In today’s economic situation, regular home buyers may postpone purchasing real estate when considering price increases compared to their earning potential. Many are willing to wait and believe that this upsurge in real estate prices will be followed by a downward trend. Judging the ratio and trends of changing nominal market prices and prices in real terms is a crucial exercise.
The number of new construction projects registered in the first quarter of 2023, was the lowest seen in the last 10 years. Considering this significant decline, it is evident that the market has set limits. Currently, it is not clear whether the construction industry’s potential excess capacity will have a consolidating effect, or whether these capacities will find their opportunities in other markets.
In Hungary, the share of imported construction materials remains at around 50%, which makes projects expensive. Do you expect more government support for local production in the medium term?
This is a good moment for the government to intervene, but any steps taken should be planned with the goal of creating a more effective and sustainable construction industry. I think direct intervention in the local construction materials production market is a double-edged sword and may influence the usual rules of this sector. But may I refer to one of our survey conclusions emphasizing the need for more detailed investigations and for spending more time on project modelling and preparation? More support should be given to innovative solutions in the construction industry and to research activities aimed at reducing both carbon construction materials and production processes.
The role of government support in building the future is crucial. While the results of such support for innovation in technology and education may be modest in the medium term, it will certainly have a significant impact on the sustainability and performance of the Hungarian construction industry in the longer term. This is the only way to close the existing gap of effectiveness between the CEE average and that of local construction companies which are, unfortunately, considered the least productive in the region.
Modular or offsite manufacturing is on the rise in developed countries. How about Europe as a whole and the CEE in particular?
There is a long history in the US of offsite manufacturing, mainly in the residential segment. But when mentioning modular manufacturing in Europe and the CEE, most people picture prefabricated 10-story mass-produced residential blocks. Most traditional construction activities take place on-site, with construction materials being delivered there to workers with the necessary equipment to produce what is needed.
Modular construction is different. Many survey participants referred to the opportunity of fully monitored and controlled manufacturing schemes and seemed ready to utilize technological solutions from other industries. If certain stages of the construction process are executed in factories under regulated conditions, this would result in a significant reduction in energy consumption and wasted materials.
It may sound strange, but a factory producing modules designed for any type of building could look very similar to an automotive production plant. It could also result in a new level of building quality, while positively impacting all ESG expectations.
According to our survey, engineering and construction companies see that not more than 20% of the projects would benefit from the application of modular or offsite manufacturing today. It is a very optimistic vision of today’s industrial environment, because to deliver on its full potential modular construction requires strong vertical integration across the project delivery lifecycle, with many participants involved.
Modular manufacturing requires changes throughout the whole process, from design and planning to construction execution and sales activities. Consumer prejudice toward prefabrication—and indeed any non-traditional structures—changes very slowly in our region. But developers, engineering and construction companies see the advantages and are ready to take the first steps.
Do you agree that shortages in skilled labour may hamper a significant move towards a much-needed restart of the industry in the CEE and Hungary? How about imported labour from non-EU countries? Does it help in the long run?
Yes. I agree and hope that the tendencies mentioned earlier will result in a different construction industry relatively soon. With digitalization, AI and the application of robotics, modular construction should reduce the size of and need for the onsite labour force. In parallel, there will be an increasing need for a better quality labour force.
Construction materials are produced on several continents, and importing these materials is an everyday practice. The workforce is part of the global economy, whether considered in real physical terms or internet-based digital means.
I don’t regard imported labour from non-EU countries to be a challenge for the construction industry—nor, for that matter, other industries, many of which (together with service segments) provide or are obliged to provide global opportunities for foreigners and integrate “imported” labour force to their business.
Supporting the development of technology, sustainability and the performance of the construction industry requires educated and skilled workers who speak the language of “digitalization.” To achieve the goals of a rebooted industry, any “imported” labour should understand this language, too.
ESG brings increasing scrutiny and compliance requirements and puts pressure on companies to reduce their carbon footprint. Do they do their job in this respect?
Up to half of carbon emissions are produced before a building is operational. So, the responsibility of the construction industry is huge. According to our global survey, 54% of the company leaders fully understand the benefits of ESG, which doesn’t just carry requirements set by regulatory frameworks—it also becomes a reputational issue. These company leaders cannot do it alone. For example, the price and availability of renewable energy used for producing construction materials and used during construction works are not fully under their control. But they are concerned and dedicated.
Companies are at very different levels of maturity in terms of ESG compliance. Data collection is very rudimentary even at some large companies, although this is only the first step in enabling footprint assessment and strategic planning.
To fulfil the reporting requirements and move towards long-term ESG goals, many companies are extending their in-house competencies with ESG Working Groups and introducing digital systems such as Energy Management Systems. Large companies must act soon to prepare themselves for reporting their performance in line with the Corporate Sustainability Reporting Directive for the financial year ending 31 December 2024. Of course, there is still plenty to do.
Most of these activities require capital investments. Though companies understand the need to act and have started to do so, there is still uncertainty concerning the potential ways these extra investments and costs will be covered by the market or by other institutional participants.
Digitalization is of the utmost importance for the construction sector. What lies beyond that? What are the latest results in using various PropTech achievements?
It is very difficult to name the latest one. PropTech, by definition, is dynamic, disruptive, independent and brave, and it happens every day. Instead, with sustainability in focus, I expect radical innovations in low-carbon materials, alongside other new concepts that will enable the construction industry to deal with existing building stock.
Market prejudice is evident when a developer wants to rehabilitate an existing property. I also expect radical PropTech solutions to emerge, making the reuse of buildings popular and desirable among regular market participants. I don’t know how it can be done, but perhaps PropTech innovators do.