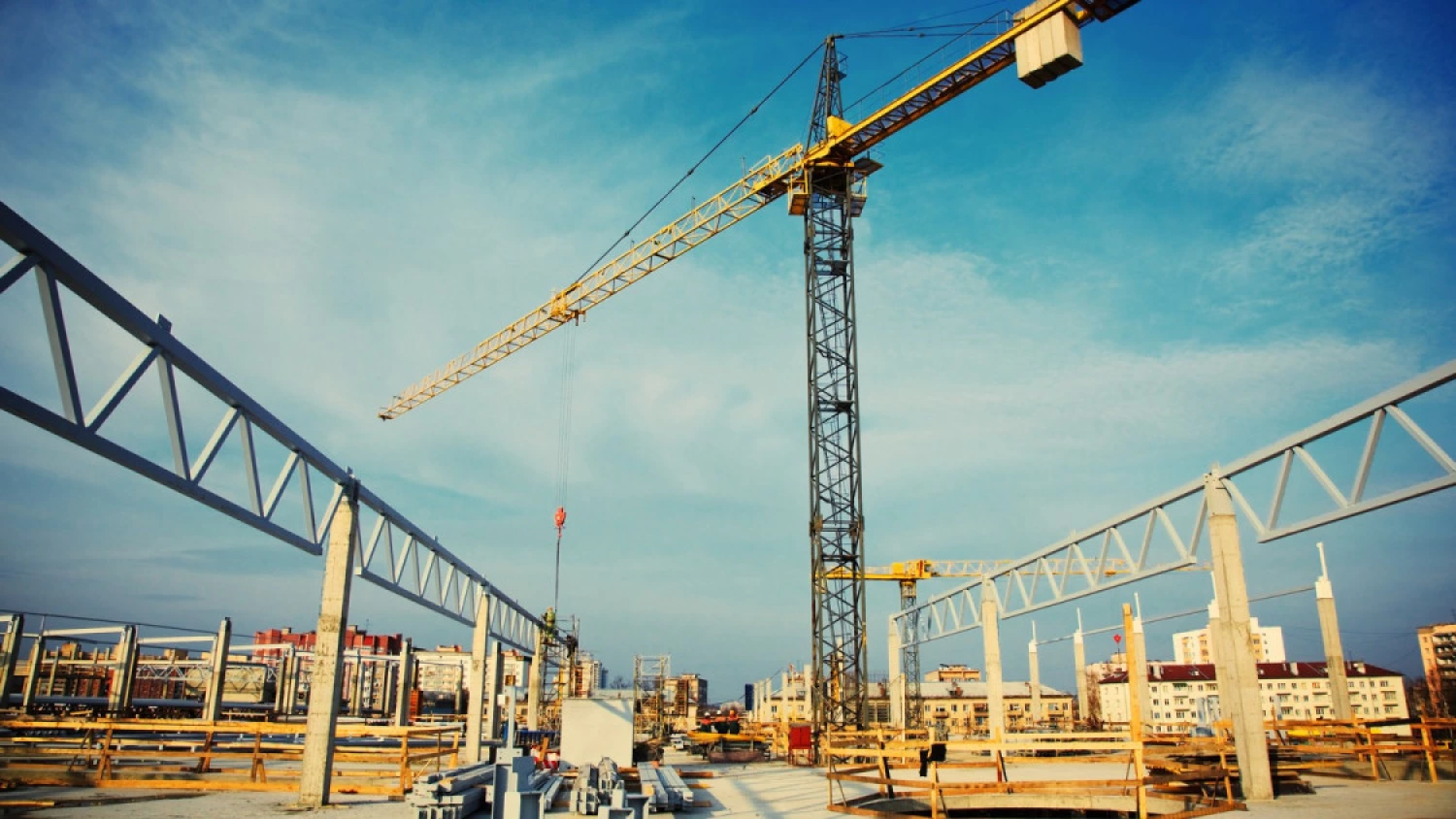
According to the UK analyst of Euroconstruct, Harvir Dhillon, material shortages have plagued the construction industry over the past few months. In tandem with rising inflation, global construction activity has experienced a supply-side shock that looks set to persist well into 2022. Disruption in the supply chain has been driven by a number of factors, from the constrained capacity of sawmills and steel mills to environmental factors such as the forest fires seen in major timber exporters like the United States and Sweden, to name but a few.
Construction activity in the EU: Austria leading the way
On the face of it, high demand for construction materials in the aftermath of a pandemic should be rather encouraging. A booming construction sector has shown its resilience following initial shutdowns in many countries. Construction activity in the EU rose by 14% in the three months to June, relative to the same period in the previous year. In the Euroconstruct network of countries, three countries have exhibited particularly exceptional growth since the onset of the pandemic. Construction output, in the year to 2021 Q2, grew 21% in Austria, 38% in France and an impressive 53% in the UK. The UK’s performance, thus, has been entirely in step with Boris Johnson’s mantra of Build Back Better.
Building material shortages: causes and consequences
However, despite experiencing somewhat of a boom in activity since, it is precisely because of the pandemic that material shortages have come to the fore. Production and distribution issues in significant global producers and exporters have meant record price increases. According to Drewry’s composite World Container Index, the cost of a 40ft container across major routes has risen to $10,000, having been around $1,500 before the pandemic. This almost seven-fold increase in shipping costs has been unprecedented, with the blocking of the Suez Canal and more recent port shutdowns in China providing notable hiccups in freighter travel.
These price increases have manifested not just in input prices but less obviously in output prices, where suppliers have been passing on rising input costs further down the supply chain. The graph above shows the evolution of prices within the construction sector; indeed, material input prices grew 2.7% (q-o-q) in the first quarter of 2021 and output prices by 1.3% over the same period. Shortages have been particularly troubling for construction markets such as Germany, France, the UK, and Italy with the effect being to deplete inventories, increase lead times as well as contract disputes.
Building materials seeing the sharpest price rises
The Department for Business, Energy & Industrial Strategy (BEIS), in the UK, keeps a track of the prices of construction materials. Their data for July show that the materials exhibiting the strongest price growth compared to 12 months ago are concrete rebar (59% higher than a year ago), fabricated steel (65% higher) and imported plywood (82% higher). These eye-watering figures lay bare the swift nature of the pace of change in prices the industry has had to become accustomed to in recent months.
Demand for these materials has soared for a multitude of reasons. It is the civil engineering sector that has particularly been driving forward growth in construction in the UK, but these naturally bigger projects are also more material-intensive. The ramping up of work on HS2 and Crossrail are a couple of notable examples. The pandemic has also brought with it changing consumer preferences. The Work From Home revolution and experience of lockdown has meant that space has become more desirable. Combined with a lack of spending opportunities and the resultant build-up of household savings, demand for home improvements was ignited. Moreover, it comes as no surprise that private sector renovation activity in the housing sector has seen considerable growth over the past year.
Driver shortage
Another stranglehold on logistical activity within the UK, likely to worsen the materials shortage over the coming months, has been the pecuniary impacts of the UK’s disintegration from the European Union, otherwise known as Brexit. Not only have import tariffs increased costs, a Heavy Goods Vehicle (HGV) driver shortage has meant that the delivery of materials has become increasingly delayed. A survey by the Road Haulage Association of hauliers suggests the top two reasons for the shortage can be ascribed to drivers retiring (hauliers have an average age of 55) as well as the UK leaving the EU. Estimates now suggest the shortage in drivers amounts to around 100,000. This problem is not limited to the British Isles, however, with research group Transport Intelligence suggesting the shortage in HGV drivers across mainland Europe could be up to 400,000.
What to expect
Further, a “normalisation” or reversion to pre-pandemic prices is unlikely in the near term and possibly even in the mid-term. Price pressure will inevitably alleviate as the global economy returns to normal, and production constraints are eased, but the impact of the materials shortage crisis will continue to resonate well into next year, posing risks for the ongoing recovery of the construction industry and threatening to delay many projects across the network.