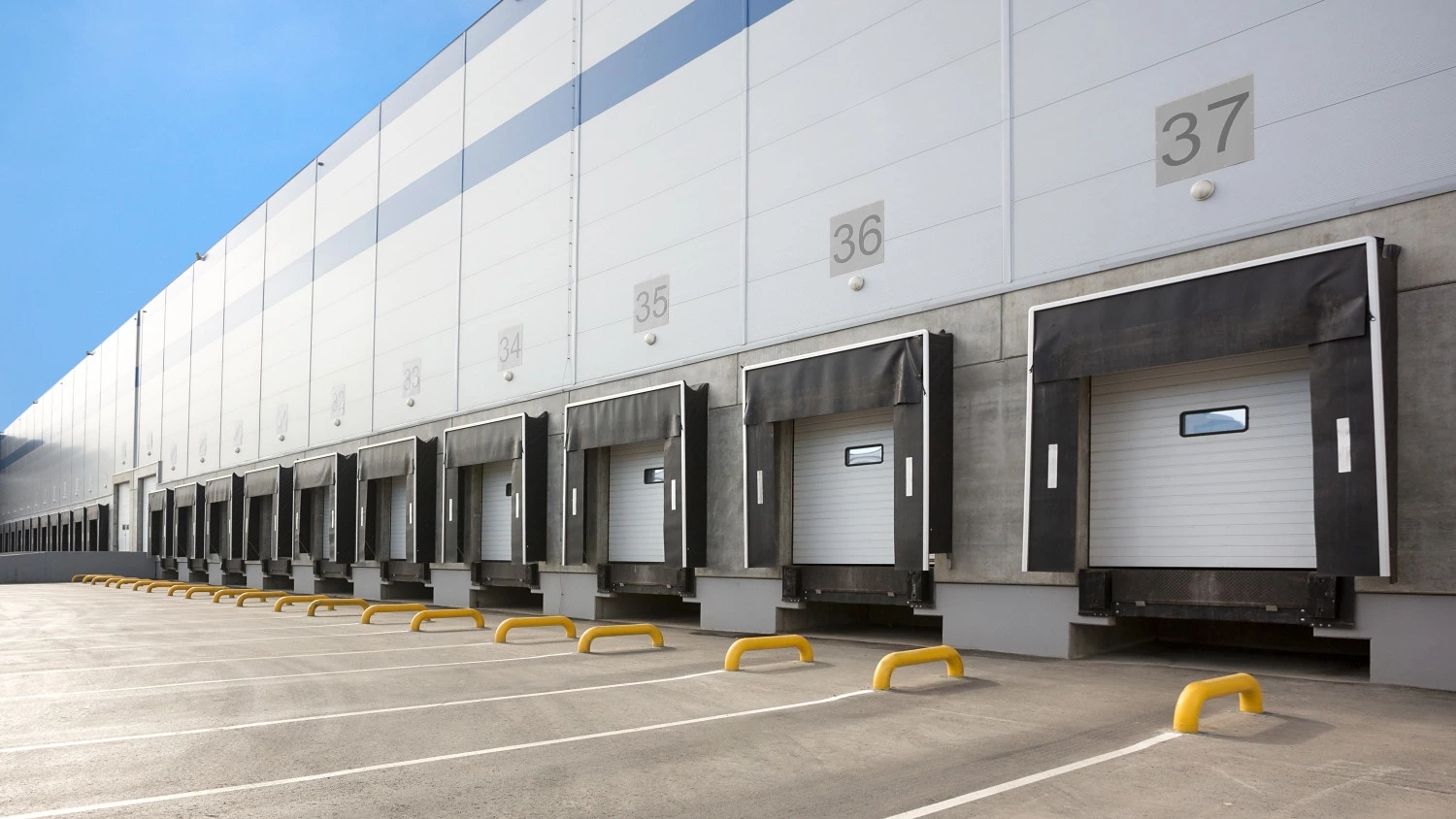
Some companies are choosing to relocate production plants from Asia to Poland to diversify business activity and shorten supply chains. On the other hand, western firms are setting up factories in Poland to bring operating costs down and take advantage of a range of benefits with which individual regions want to attract investors, say experts from Cresa Poland.
Supply chains between Asian production plants and European markets have recently been at high risk of disruption. Some companies are therefore increasingly eyeing Poland, which they see as a stable and safe country that allows for risk diversification.
“As companies don’t want to rely exclusively on supplies from Asia, they are considering shifting production lines to Europe,” says Jakub Kurek, Associate Director in the Industrial and Warehouse Department at Cresa Poland. “Although this trend began well before the outbreak of the Covid-19 pandemic, lockdowns and border closures have exacerbated the issue. However, despite the attractiveness of Poland as a manufacturing location on the European continent, important decisions such as relocating production or logistics function to new territories are very complex, require thorough analysis and time for implementation. Therefore, we should not be under the impression that a mass migration of production operations from Asia to Poland will happen imminently. Poland will undoubtedly benefit but this will take some time to materialize.”
Relocations from the West
The relocation of manufacturing from Asia is not the only direction of travel for businesses. Benefiting from lower industrial and warehouse rents and labour costs, companies are also shifting factories from Western Europe, U.K., France and Germany in particular, to Poland, which, of course, is not the only destination on their radars. Poland’s main rivals in this field are the Czech Republic, Slovakia, Hungary, and Romania.
One example of a recent relocation from Germany was the transfer of a production plant for Dywidag Systems International to the South of Poland. With the assistance from the advisors at Cresa Poland, the company leased 24,000 sqm of industrial and social space in Ruda Śląska, where it launched production of post-tensioning and stay cable systems. Ruda Śląska has the advantage of not only its proximity to the company’s current headquarters, but also of being a business-friendly town with an excellent and continuously improved transportation network and a large pool of labour.
Logistical heart of Europe
“Poland has grown into a regional leader for manufacturing, best illustrated by the number and size of new projects it has recently attracted. With its central location and well-developed network of national roads and motorways, it has, in a sense, become the logistical heart of Europe. Manufacturers are able to swiftly and easily execute deliveries from Poland not only to the East, but also to other European markets. New investors particularly appreciate Poland’s large labour pool with qualified and high-skilled employees available for any manufacturing sector,” says Michał Kozar, Senior Advisor, Industrial and Warehouse Department, Cresa Poland.
Manufacturing in Poland offers a very attractive value proposition compared to Germany, France or Italy, which has led to a heightened interest in setting up production plants in our country.
“Average industrial rents here are about 30-40 percent lower than in the West, there are about a dozen large developers active on the market and more than two million square metres of industrial and warehouse space is under construction across Poland. Manufacturers will have a large choice of industrial facilities in terms of both location and technical specification,” says Jakub Kurek. “High availability of engineers and other specialists is also important to manufacturers. In addition, wages in Poland are much lower than those in Western Europe. Investors can also benefit from tax exemptions in the Polish Investment Zone, which in 2018 was extended to the whole of Poland.”
BTS or BTO?
The decision to lease versus own real estate is very company-specific, based on a number of different factors and also dependent on property and economic cycles. On the one hand, many manufacturers opt to invest purely in their core business and not in the real estate they occupy for their production functions. In this instance, the preference for manufacturers is not to own but to rather sign a long-term lease for a new Build To Suit facility. This provides an element of flexibility should the tenant decide to vacate, relocate or change the location of its operations.
On the other hand, some manufacturers see their production plants as strategic assets, core to their main production operations and therefore decide to own these buildings. In many cases, significant financial investment is undertaken for the internal fit-out of the building to accommodate production technology, automation, racking and other costly installations tailored exactly to the needs of their manufacturing and logistics processes. “The trend towards Build To Own (BTO) projects intensified from the start of 2019, when new tax and accounting regulations IFRS 16 took effect. As a result, many companies with access to cheap capital, will favour BTO projects over long-term leases purely from an accounting perspective,” says Michał Kozar.
Great potential and lots to do
International companies opening factories in Poland are largely from such sectors as automotive, electro-technical (electronics and home appliances), chemical, and construction. One example is Stellantis with development projects under way in Tychy. Stellantis is a new manufacturer formed by the merger of Fiat Chrysler Automobiles and Peugeot Citroen Opel DS. Polish and international subcontractors are waiting for winning tenders to be announced and are planning to build factories in the vicinity. Industrial and warehouse developers have already secured development sites in this location.
“Poland is well-positioned to support those manufacturers planning to locate new production functions in the country. Its central position in Europe, availability of high-skilled engineers, industrial and warehouse developers ready to invest in the country, and various attractive forms of financing contribute to its attractiveness as a manufacturing location. There is still, however, a lot to be done in this area, especially with regard to innovation, automation, ESG and improving production efficiency.
Poland was generally viewed as a maturing industrial market in Europe for many years however the supply and demand dynamics over the last 5 years in particular underpin the importance of the country on the European industrial map and also its attractiveness for companies looking to expand their global operations and footprints,” concludes Jakub Kurek.