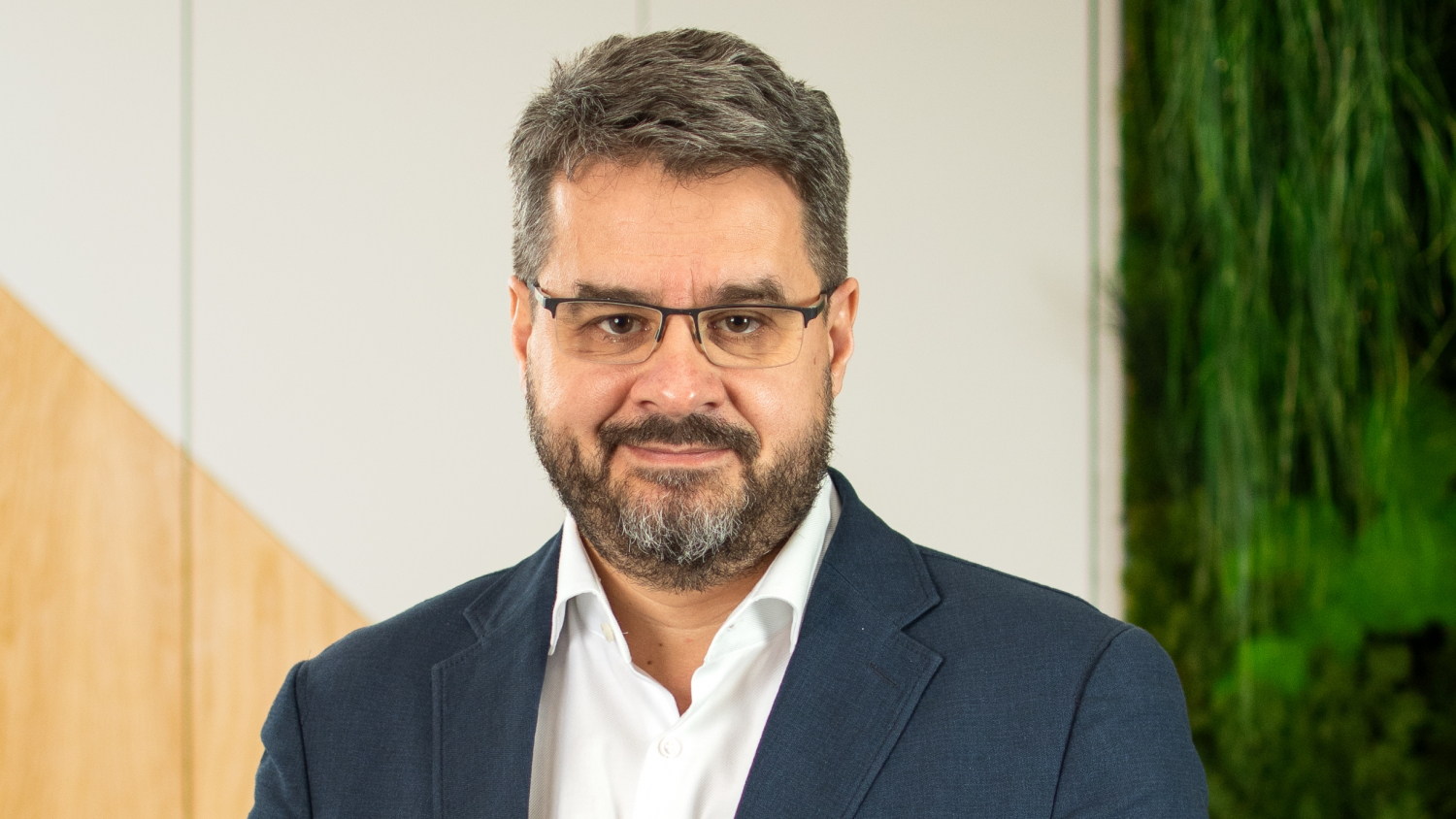
Cătălin Rotaru, CEO of Romanian company THETA Furniture & More, spoke to Property Forum about the company’s expansion strategy in the healthcare, HoReCa and education segments, as well as the competitive advantages of operating a custom-made furniture factory in Romania.
This interview was first published in Property Forum’s annual listing of "The 50 most influential people on Romania’s real estate market”.
What are your plans for 2023 and how did the company perform last year in terms of business and customer portfolio?
Despite the challenges generated in 2022 by the greenfield investment in our new custom-made furniture production plant, last year we achieved a turnover growth of over 10%.
This year’s results are already visible, the 1st quarter being closed with double production compared to previous years. Considering the on-going projects, we estimate that we will maintain this growth rate throughout 2023, securing our plans to increase the turnover by more than 30%.
Otherwise, we intend to expand partnerships with other fit-out service providers in the market, taking into account the thoughtfulness aspect that defines us in delivering custom-made furniture production and installation services. Since last year, we have strongly developed projects in the health and HoReCa segments, increasing their share to over 40% of the company’s portfolio.
What are the current trends in the interior design market from Romania?
Interior design and fit-out trends in the office and commercial market for 2023 in Romania are aligned with the global ones, having as priority the creation of a healthy and wellness-promoting work environment. Sustainability is at the top of the trends in 2023, materials such as wood, glass, stone, or metal being frequently used. Wellness design is conveyed in spaces with natural light, achieved by maximizing the use of glass walls and implementing high-tech digital solutions and agile workspaces, combining private and shared work areas with neutral relaxation areas.
What are the predominant industries from THETA’s client’s portfolio? Are there certain sectors that have an increasing volume of demand?
Since its establishment in 2008, THETA Furniture & More has delivered over 400,000 sqm of interior spaces, for more than 1,800 clients, local and international companies, with spaces located in the most important office areas of Bucharest.
While in the last 2 years office fit-out or refurbishment projects have predominated, health and HoReCa industries recovered strongly. In the context of office space slow-down, having our own production facilities allowed us reallocation of the production and implementation capacity to other areas such as medical, HoReCa and education. So far, the company has delivered over 1200 office spaces, 500 commercial spaces and 120 HoReCa spaces.
How have the requests for office fittings changed after the pandemic? What are the elements that companies are counting on, especially in light of the hybrid work style?
The dynamic of the companies’ activity in the post-pandemic period has also been reflected in changed specifications of the bidding process for spaces that need interior design, both in terms of space area and the technical fit-out equipment.
The hybrid work system combined with “work from home” has led to the decrease of workspaces or push demand for higher efficiency and the increase of quality requirements.
Thus, the offices were re-compartmentalized from open space areas with adjoining offices, in modular offices that offer maximum flexibility, as well as the updating of the ventilation installations by installing high-performance air filters.
The elements that companies rely on in the workspaces are those that help them in the process of persuading their employees to return to the office in large numbers, offering them a “city-in-city” concept, with co-working spaces working but also private, with relaxation areas & connection to urban life and with easy access to related services.
What are the advantages of owning a furniture factory in the country and how is the “Made in Romania” label perceived in the market?
Owning a custom-made furniture production plant is our main differentiator in the interior design market, and it certainly brings us many advantages. The increased production capacity of the factory and our own installation teams, allows us to be very flexible in allocating, throughout the project, important resources for rapid and timely production and implementation of large custom-made furniture volumes. In the process of an interior design project implementation, the final phase is the installation of the custom-made furniture, and we can assign important resources at the right time.
In the context of the international crises that have occurred in recent years, with a major impact on supply chains, the existence of the local factory and suppliers of raw materials has eliminated many of the delivery uncertainties that arise in the case of external procurement.
The fact that we benefit from a strong furniture industry in Romania is also to our advantage through the existence of a large portfolio of suppliers and a recruitment pool of local, highly skilled labour. In external projects where we supply products with the Made in Romania label, we benefit from the quality awareness of the local furniture industry.
How many employees does the company currently have? Are you planning to recruit specialists for certain positions?
The company currently has 130 employees, out of which more than 100 are working at the production plant in Păulești, Prahova and the rest at the headquarter, in Bucharest.
Given the high degree of automation in the manufacturing flow, more than 25% of the factory’s staff are designers and machine operators who ensure the computer-aided production of the structural elements for the furniture components. The increasingly demanding requirements of our customers, together with the increase in manufacturing capacity, have led to internalizing of new processes: metal processing, upholstery, and composite materials processing (Corian, Krion, Staron, Hanex – including thermoforming), also hiring the necessary staff.
For the next three years we estimate to exceed 150 employees, completing the team with qualified specialists both in the production area, skilled in the management of automated processes and factory machinery, in project implementation & management, as well as in commercial development of the company.
What is the biggest challenge and opportunity in running a company in the interior design segment?
The biggest challenge we face is managing the fluctuations of the entire procurement and implementation process, generated either by macroeconomic situations, or changes in project design, or in initial budgets or execution deadlines. Symmetrically, we have a great opportunity by having the possibility to control the execution and implementation process
Much better, as we offer all products and services at an integrated level. For a client, working with THETA as an integrated service supplier, responsible for the entire process of setting up the space, offers him the advantage of obtaining a cost reduction of 15-20% and securing the timely implementation of the project.
Considering the slow-down of the office market from last year, our position as a one-stop solution supplier with integrated fit-out services, a complex portfolio of standard furniture suppliers and our own factory of custom-made furniture gives us the advantage of accessing several projects in industries which have a very high development potential: health, HoReCa and education.